When your project demands corrosion resistance, exceptional strength, and precise fabrication, you need a partner who understands stainless steel's unique properties. At Accurate Metal Fabricating, we've spent decades perfecting our stainless steel fabrication processes to deliver components that meet your specifications.
Our Stainless Steel Fabrication Capabilities
Precision Cutting Services
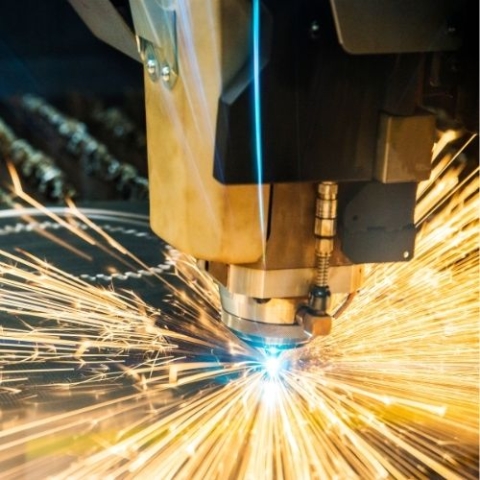
Our laser cutting services handle stainless steel with exceptional edge quality. We operate three advanced laser systems—the Amada Pulsar LC 1212 A4 CO₂ laser and two 6kW Bystronic fiber lasers. The fiber lasers excel at cutting stainless steel rapidly while maintaining minimal heat-affected zones, preserving the material's corrosion resistance near cut edges.
Our Bystronic laser tables, with integrated nitrogen generators, deliver smooth, oxide-free edges on stainless steel for complex geometries and thicker materials. The automated material handling on our BySmart Fiber allows us to run your stainless parts 24/7, ensuring fast turnaround even on large orders.
Forming and Bending
Stainless steel's tendency to spring back during forming requires precise calculations and specialized tooling. Our 17 press brakes—ranging from 40-ton Amada units to 175-ton Cincinnati machines—feature dedicated stainless steel tooling sets that account for this spring back, ensuring your formed parts meet dimensional requirements on the first run.
Our newest addition, the Amada EGB 1303 with 130-ton capacity and advanced CNC controls, excels at forming thicker stainless steel components. The offline programming capability through VPSS 3i software allows us to simulate complex bends before touching material, reducing setup time and ensuring accuracy.
We form stainless steel components up to 10 feet long. Our operators understand how different grades—from 304 to 316L to duplex alloys—respond to forming operations.
Welding Excellence
TIG welding remains our primary joining method for stainless steel fabrication. This process provides the control needed for aesthetic welds in certain applications.
Our IPG Photonics LightWeld XR laser welder delivers exceptionally clean welds with minimal heat input for precision applications. This technology excels on thin stainless steel where distortion control is critical. The concentrated energy creates narrow, deep welds while preserving the material properties adjacent to the joint.
Our robotic welding cells, including Motoman and Lincoln systems, handle high-volume stainless steel production with consistent quality. These automated systems maintain precise arc parameters and travel speeds, ensuring uniform weld penetration across thousands of parts. Every weld receives proper back-purging when full penetration is required, preventing oxidation that could compromise corrosion resistance.
Alternative Processing Methods
Beyond laser cutting, our seven CNC turret presses provide cost-effective solutions for stainless steel parts requiring multiple holes or formed features. The Amada turret press fleet, including our EMZ 3610 NT and dual Pega-357 units, efficiently punches patterns in stainless sheets while maintaining excellent hole quality.
For applications where laser cutting isn't optimal, turret punching offers advantages in specific geometries and production volumes. Our automated tool changers and 30-ton capacity machines handle stainless steel efficiently, particularly for parts with repetitive hole patterns or louvers.
Surface Finishing Excellence
Our powder coating line provides superior finishes for stainless steel components requiring enhanced durability or specific colors. As an authorized AAMA 2603, 2604, and 2605 applicator, we ensure your stainless parts receive consistent, high-quality coatings.
The 5-stage wash system prepares stainless steel surfaces, ensuring optimal paint adhesion even on this challenging substrate. With over 1,000 color recipes available and the ability to apply specialized coatings like zinc-rich primers, we match your exact specifications. Our standard 2-4 mil coating thickness is tested throughout production runs.
Food and Beverage Processing
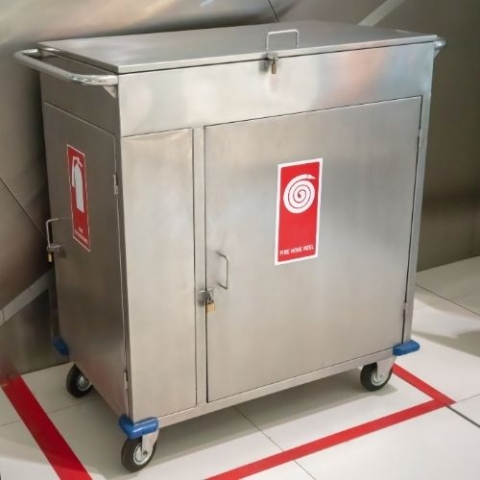
The food industry demands stainless steel fabrication that meets strict sanitary standards. We use 304 and 316 stainless steel to fabricate portable carts, equipment enclosures, range hoods, and table tops. Portable stainless steel carts require careful attention to both functionality and cleanability. We design these with fully welded frames, proper drainage slopes, and smooth surface transitions. Our range hoods combine structural integrity with polished finishes that withstand daily cleaning in commercial kitchens.
Industrial Lighting Applications
Industrial lighting manufacturers rely on our stainless steel fabrication for fixtures that withstand harsh environments. Stainless steel's corrosion resistance makes it ideal for outdoor fixtures, high-moisture areas, and facilities with chemical exposure.
We fabricate housings, reflectors, and mounting brackets that combine structural strength with aesthetic appeal. The non-magnetic properties of 304 and 316 stainless steel make these grades perfect for specialized lighting applications where magnetic interference must be minimized.
Our powder coating capabilities allow us to apply durable finishes to stainless steel lighting components when specific colors or enhanced weather resistance are required. Combining stainless steel's inherent durability and our high-quality coatings ensures fixtures that maintain their appearance for decades.
Surface Finishing Excellence
Our powder coating line provides superior finishes for stainless steel components requiring enhanced durability or specific colors. As an authorized AAMA 2603, 2604, and 2605 applicator, we ensure your stainless parts receive consistent, high-quality coatings.
The 5-stage wash system prepares stainless steel surfaces, ensuring optimal paint adhesion even on this challenging substrate. With over 1,000 color recipes available and the ability to apply specialized coatings like zinc-rich primers, we match your exact specifications. Our standard 2-4 mil coating thickness is monitored throughout production runs.
Choosing the right stainless steel grade impacts both performance and cost. Let me share insights on the common grades we work with:
- 304 Stainless Steel serves as the workhorse for general corrosion resistance. Its 18% chromium and 8% nickel content provides excellent formability and weldability. We recommend 304 for indoor applications and environments without chloride exposure.
- 316 Stainless Steel adds molybdenum for enhanced corrosion resistance, particularly against chlorides. This makes it ideal for marine environments, chemical processing, and anywhere salt exposure occurs. The 2-3% molybdenum content justifies the higher cost in demanding applications.
- 316L Stainless Steel features lower carbon content, reducing carbide precipitation during welding. We specify 316L for welded assemblies in corrosive environments where post-weld heat treatment isn't practical.
We work with duplex and super duplex grades for extreme environments. These materials combine austenitic and ferritic properties for exceptional strength and corrosion resistance.
Design Considerations for Stainless Steel
Stainless steel fabrication starts with proper design. We help optimize your designs for manufacturability while maintaining functionality.
Joint design affects both cost and performance. We recommend minimizing weld length while ensuring adequate strength. Proper fit-up becomes critical with stainless steel—gaps that might be acceptable in carbon steel can cause problems with stainless welding.
Surface finish requirements drive fabrication decisions. If you need a #4 brushed finish, we'll plan our process to minimize handling marks. We'll ensure proper weld quality for electropolished finishes to achieve uniform results.
Cost Factors in Stainless Steel Fabrication
Understanding cost drivers helps you make informed decisions about your stainless steel projects. Material costs typically represent 40-60% of total project cost, compared to 20-30% for carbon steel projects. This higher percentage reflects stainless steel's premium pricing.
Processing costs also increase due to slower cutting speeds, specialized tooling, and additional handling requirements. However, stainless steel's durability often lowers lifecycle costs through reduced maintenance and longer service life.
We help optimize costs through design refinements. Switching from 316 to 304 stainless sometimes provides adequate performance at significant savings. Other times, investing in better surface finishes during fabrication eliminates costly field modifications.
Perforated Stainless Steel Solutions
Our sister company, Accurate Perforating, provides perforated stainless steel that integrates seamlessly with our fabrication capabilities when your project requires perforated stainless steel. They perforate stainless steel in thousands of different patterns, handling materials from 24 gauge to 1/4" thickness and widths up to 60".
This partnership creates a streamlined workflow for your perforated stainless steel projects. Accurate Perforating produces the perforated sheets, coils, or blanks to your exact specifications and then transfers them directly to our facility for fabrication. Whether you need perforated stainless steel enclosures for ventilation, decorative architectural panels, or functional components for food processing equipment, we coordinate perforation and fabrication under one production plan. This integrated approach reduces lead times, ensures quality control throughout the process, and provides you with a single point of contact for your complete project.
Why Choose Accurate Metal Fabricating
Our comprehensive in-house capabilities benefit your stainless steel projects. With fabrication and powder coating under one roof, we streamline your supply chain. Parts move directly from fabrication to finishing without the delays and risks of outside processing.
Contact our sales group about your stainless steel fabrication requirements. Whether you need guidance on material selection, have questions about our capabilities, or want to discuss a specific project, we're here to help.