Roll Forming vs. Press Braking: What to Consider for Your Next Fabrication Project
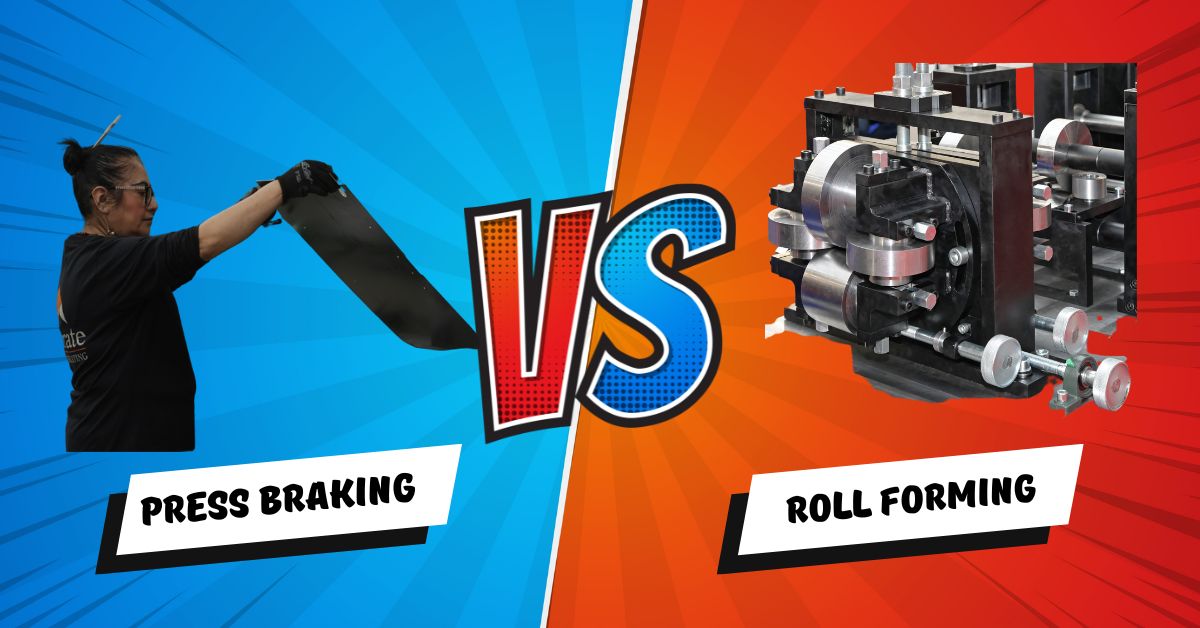
Precision is key in metal fabrication. From architectural components to medical enclosures and industrial housings, a project's success often hinges on one critical choice: selecting the right forming technique. In fact, that decision can influence everything from production speed and cost to the overall quality and performance of the final product.
Two of the various forming methods available are widely used: press braking and roll forming. Each has its own advantages, but the right choice depends largely on your project's specific demands. Get ready for a battle to the bitter end—roll forming vs. press braking!
What is Press Braking?
Press braking is a highly controlled bending process ideal for precision fabrication. This metal-forming process uses a hydraulic press and a die set to bend sheet metal into specific angles or curves. The sheet is clamped between a punch and a die, and pressure is applied to create the desired bend.
This method is ideal for small- to medium-volume production and especially suits projects that demand precise bends, multiple angles, or tight tolerances. Its versatility and accuracy make it a preferred choice for creating components across product lines, including lighting components, EV Charging, and custom enclosures.
What is Roll Forming?
Roll forming is a continuous, high-speed process best suited for uniform, high-volume parts. It involves passing a long metal strip through a series of roller dies that gradually shape the metal into a desired profile. Roll forming is less flexible when it comes to customization. It’s not ideal for intricate parts or components requiring precise, varied angles—areas where press braking excels.
Why Press Braking Is the Better Option for Most Projects
Press braking is often the top choice for projects where precision, customization, and flexibility matter most. The following are some of the reasons for the process's wide popularity.
-
Precision and Customization: Press braking offers exceptional control over bend angles and shapes for custom-designed components. Whether you are fabricating enclosures, brackets, or medical housings, the ability to fine-tune every detail is invaluable.
-
Complex Parts: Press braking delivers the customization needed to match demanding specifications for components that require intricate bends, precise tolerances, or non-standard geometries.
-
Flexibility for Small Batches: Roll forming requires significant setup time and cost, making it more suitable for large-volume runs. In contrast, press braking offers greater agility for low to mid-volume production, allowing you to fabricate unique parts without the overhead associated with roll forming.
-
Versatility for Complex Shapes: Do you need multiple bends at tight angles? Or a complex design in varying dimensions? Press braking is built for such challenges. Its adaptability makes it the ideal technique for components with non-linear geometries and asymmetric profiles that would be difficult or impossible to replicate with roll forming.
-
Quality Control and Accuracy: Consistency is crucial in data centers, power generation, and the military. Press braking provides higher levels of repeatability and tighter quality control, reducing the risk of defects and ensuring that each part performs as intended.
-
Faster Turnarounds for Tight Deadlines: Press braking involves minimal setup compared to roll forming, making it ideal for projects with aggressive timelines. When speed is critical, but quality still matters, press braking delivers both, helping you meet deadlines without sacrificing precision.
Why Accurate Metal Fabricating Prefers Press Braking
Choosing the right forming method in metal fabrication is crucial to achieving the best results. While roll forming excels in large-scale, high-volume production, press braking is superior when precision, adaptability, and efficiency are essential, particularly for custom, low- to mid-volume projects. Press braking stands out for its ability to meet tight tolerances, create intricate shapes, and deliver exceptional customization.
At Accurate Metal Fabricating, press braking is more than just a technique, and it’s a cornerstone of our commitment to quality. With decades of experience, we provide custom press braking solutions for industries ranging from OEMs to medical device manufacturers. We understand the importance of precision, flexibility, and quick turnarounds, and our advanced equipment and skilled team make it possible to create high-quality parts with minimal lead times and consistent results.
Press braking is ideal if your project requires precise bends, intricate shapes, or fast delivery. With Accurate Metal Fabricating as your partner, you can trust that your designs will come to life with accuracy and efficiency. Contact our team today to learn how we can help you meet your fabrication goals with confidence.